Enhancing Efficiency with a Machine Label Applicator
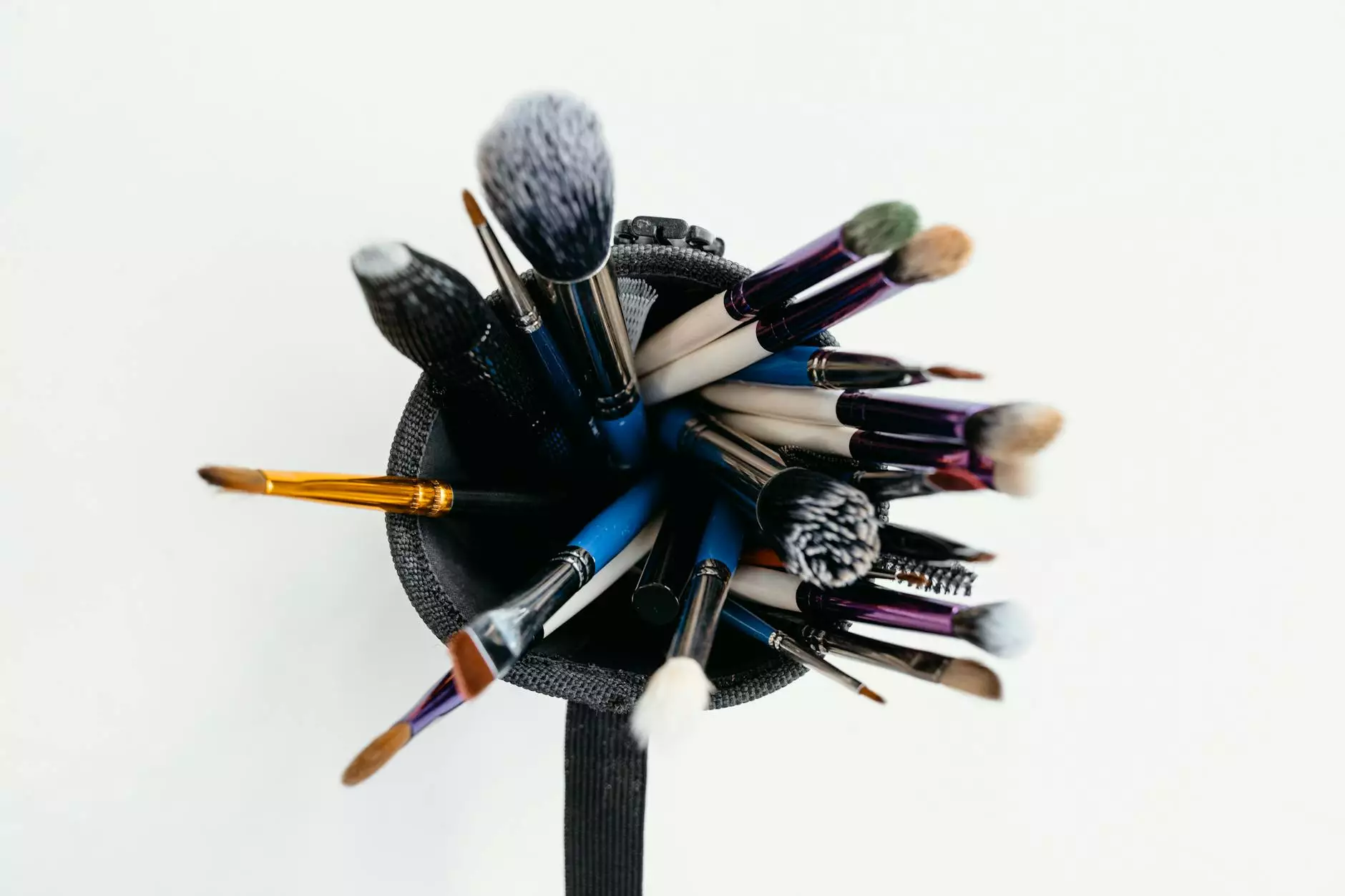
In an era where efficiency and precision are paramount in business operations, the machine label applicator has emerged as a game changer in the labeling and packaging industry. With the correct application of this technology, businesses can significantly enhance their productivity, reduce operational costs, and streamline their processes.
The Importance of Labeling in Business
Labeling is often seen as a mundane task; however, it plays a crucial role in various industries, including retail, manufacturing, and logistics. Effective labeling ensures:
- Compliance: Many industries have strict regulatory requirements that mandate proper labeling.
- Brand Recognition: Attractive and informative labels help establish and reinforce brand identity.
- Product Information: Labels provide essential information to consumers, enhancing their purchasing decisions.
- Efficiency in Operations: Well-organized labeling systems streamline workflows and prevent errors.
What is a Machine Label Applicator?
A machine label applicator is an automated device designed to accurately apply labels to various products, packaging, and containers. These machines are available in various configurations, capable of handling a range of products from small bottles to large boxes. They utilize advanced technology to ensure that labels are applied consistently and efficiently. The primary components of a labeling machine typically include:
- Label Roll: The source of labels that the machine will apply.
- Dispensing System: Mechanism that pulls the label from the roll and prepares it for application.
- Application Head: The part of the machine that applies the label to the product.
- Control Panel: Allows operators to manage settings such as speed and label placement.
Types of Machine Label Applicators
There are several types of machine label applicators, each suited for different product types and production environments:
1. Manual Labeling Machines
These machines require some level of human intervention. They are ideal for small-scale operations or for products that have irregular shapes.
2. Semi-Automatic Labeling Machines
Semi-automatic machines enhance productivity while still requiring some manual input from operators. They are beneficial for businesses that need flexibility in labeling various product sizes.
3. Fully Automatic Labeling Machines
Fully automatic labeling machines operate with minimal human intervention. Once set up, they can process large batches of products quickly and accurately, making them suitable for high-volume production.
4. Wrap-Around Label Applicators
These machines are specifically designed for cylindrical containers. They can efficiently apply labels around bottles, jars, and other cylindrical items, ensuring that each label is perfectly aligned.
5. Front and Back Label Applicators
These applicators are used when labels need to be applied to both the front and rear of a product. They are common in food and beverage industries where branding and regulatory information must be presented clearly.
Benefits of Using a Machine Label Applicator
Implementing a machine label applicator can bring a multitude of advantages to businesses:
- Increased Speed: Automation accelerates the labeling process, allowing companies to meet high-demand production demands without sacrificing quality.
- Enhanced Accuracy: Machine applicators drastically reduce the chance of human error, ensuring that labels are applied correctly every time.
- Cost-Effective: Although there is an initial investment, these machines pay for themselves by reducing labor costs and increasing throughput.
- Consistency: Automated systems guarantee that labels are applied in the same manner each time, which is critical for brand image.
- Scalability: As businesses grow, machine label applicators can accommodate larger production runs without a significant increase in labor costs.
Selecting the Right Machine Label Applicator
Choosing the right machine label applicator requires careful consideration of various factors including:
- Production Volume: High-volume productions benefit from automatic machines, while lower volumes may suit semi-automatic or manual systems.
- Product Type: The shape and size of the product will determine the type of applicator needed (e.g., wrap-around, top/bottom).
- Label Type: Different labels (adhesive, shrink sleeves, etc.) may require different application technologies.
- Budget: Both upfront costs and long-term operational costs should be factored into your decision.
Best Practices for Using Machine Label Applicators
To maximize the efficiency and longevity of machine label applicators, businesses should adhere to the following best practices:
- Regular Maintenance: Schedule routine checks and maintenance to prevent downtime and ensure optimal performance.
- Operator Training: Proper training for machine operators can greatly enhance productivity and reduce errors.
- Quality Label Material: Invest in high-quality labels and adhesives to ensure they can withstand transport and handling.
- System Calibration: Regularly calibrate machines to maintain accuracy in label placement.
- Monitor Performance: Keep track of machine output and efficiency to identify areas for improvement.
Conclusion
In today's competitive business climate, the adoption of innovative technologies such as a machine label applicator is no longer optional but crucial for success. By improving efficiency, reducing costs, and ensuring consistent branding, these machines are a valuable asset to any business focused on growth and excellence in operations.
To learn more about enhancing your labeling processes and to find the perfect machines for your business needs, don't hesitate to explore OmegaBrand.com, where cutting-edge solutions await to elevate your operational capabilities.