Industrial Spiral Cooling Towers: Revolutionizing Refrigeration Equipment
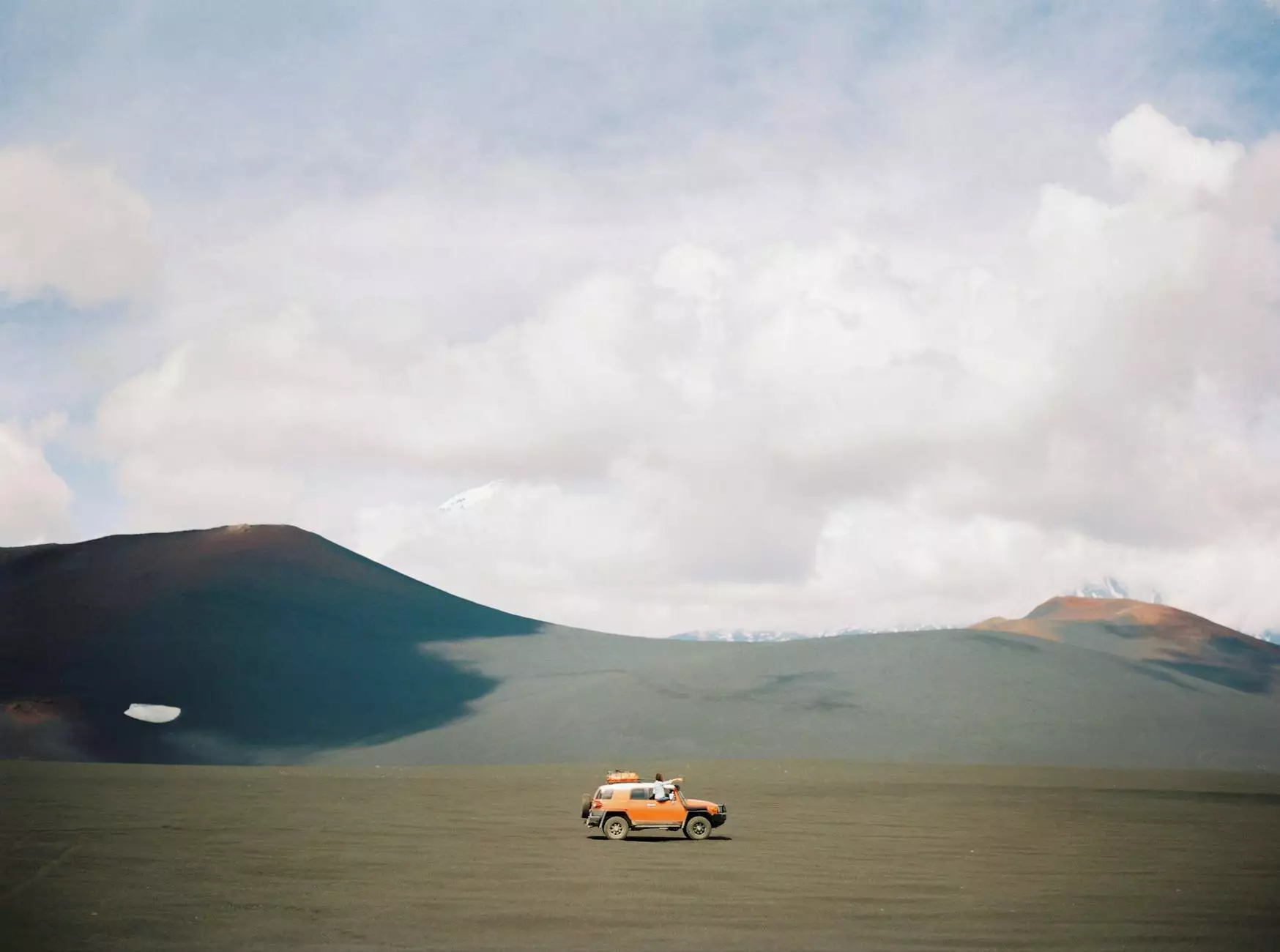
In the realm of refrigeration equipment, effective cooling solutions are imperative for various industrial applications. One of the most efficient and innovative systems currently available is the industrial spiral cooling towers. These systems exemplify optimal heat exchange and air cooling, making them essential for industries that prioritize efficiency and reliability. This article delves into the intricate details surrounding industrial spiral cooling towers, their design, advantages, applications, and maintenance, ensuring businesses like first-coldchain.com can leverage the best practices in refrigeration technology.
Understanding Industrial Spiral Cooling Towers
The industrial spiral cooling towers are designed to meet high cooling capacity requirements while maintaining low operational costs. Their unique vertical design allows for a compact footprint, making them ideal for industries where space is a constraint. Unlike traditional cooling towers, these spiral structures draw air in through a circular fan configuration, enhancing airflow efficiency and performance.
Key Features of Industrial Spiral Cooling Towers
- Compact Design: Their spiral structure maximizes cooling within a minimal area, ideal for urban installations.
- Efficient Airflow: The design facilitates a more streamlined airflow process, leading to enhanced cooling efficiency.
- Reduced Energy Consumption: These systems operate on lower energy, thus reducing operational costs significantly.
- Durability and Longevity: Built with corrosion-resistant materials, they promise a longer service life even under demanding conditions.
- Easy Maintenance: The accessible design allows for straightforward cleaning and inspections, minimizing downtime.
The Advantages of Implementing Industrial Spiral Cooling Towers
Businesses that integrate industrial spiral cooling towers into their operations stand to gain numerous advantages, including:
1. Enhanced Cooling Efficiency
The design of spiral cooling towers optimizes heat exchange processes, ensuring efficient cooling even in high ambient temperatures. This efficiency ensures that production processes remain stable and effective.
2. Space Saving
Given their vertical configuration, these cooling towers require less horizontal space compared to traditional systems. This is particularly beneficial for urban facilities or smaller industrial plants where space limitations are a concern.
3. Lower Operating Costs
With reduced energy consumption and lower maintenance costs, businesses can save substantially on operational expenses. The efficient use of energy also plays a role in minimizing carbon footprints, aligning with sustainable practices.
4. Versatile Applications
Industrial spiral cooling towers are suitable for various applications, including:
- Power plants
- Pulp and paper industries
- Chemical manufacturing
- Food and beverage processing
- HVAC systems
- Plastic and rubber production
Design Considerations for Industrial Spiral Cooling Towers
When considering the implementation of industrial spiral cooling towers, it is crucial to take into account several design factors to ensure optimal performance:
1. Load Requirements
Understanding the cooling load is fundamental. This includes calculations based on the heat load generated by equipment and the desired temperature output. Accurate load assessments lead to better selection of tower specifications.
2. Material Selection
Choosing the right materials for construction, such as fiberglass or stainless steel, is crucial for longevity and performance, particularly in corrosive environments.
3. Compatibility with Existing Systems
Industrial spiral cooling towers must be compatible with existing systems and environments. This includes considerations for plumbing, electrical connections, and overall energy efficiency goals.
4. Environmental Factors
Locations with extreme weather conditions require extra consideration for the operational reliability of cooling towers. Ensuring structural integrity and optimal functioning in various temperatures is essential.
Applications of Industrial Spiral Cooling Towers
Industrial spiral cooling towers serve a broad range of industries. Understanding these applications can help businesses better implement these solutions in their operations:
1. Power Generation
In power plants, cooling towers dissipate heat generated by turbines. Spiral designs are particularly advantageous due to their high capacity and efficiency, supporting energy generation processes significantly.
2. Manufacturing Processes
Many manufacturing processes generate significant heat. Utilizing spiral cooling towers helps maintain optimal temperatures, ensuring product quality while maximizing equipment longevity.
3. Oil and Gas Industry
The extraction and refining of oil and gas require substantial cooling systems to manage the heat produced during operations. Spiral cooling towers provide reliable performance under high-load demands.
4. Chemical Processing
The chemical industry often involves exothermic reactions resulting in heat generation. Spiral cooling towers effectively handle these heat loads, supporting safer production environments.
5. Food Processing
The food industry relies heavily on precise temperature controls. Spiral cooling towers are ideal for ensuring that processing equipment operates under optimal cooling conditions to maintain food safety and quality.
Maintaining Industrial Spiral Cooling Towers for Long-Term Performance
To guarantee long-term functionality and performance of industrial spiral cooling towers, regular maintenance is essential. Key maintenance actions include:
1. Routine Inspections
Regular inspections help in identifying any potential issues before they escalate. Checking for wear and tear on parts, as well as assessing performance under load, is crucial.
2. Cleaning and Debris Removal
Maintaining clean systems is vital to ensuring optimal performance. During routine cleaning, removing debris, algae, and scale build-up will help in maintaining efficiency.
3. Monitoring Performance Metrics
Key performance indicators (KPIs) such as cooling efficiency and energy consumption should be monitored regularly. This enables timely interventions if performance drops below standard.
4. Professional Servicing
Engaging with qualified professionals for regular checks and servicing ensures that all components are functioning as intended. They can also provide upgrades and improvements where necessary.
The Future of Industrial Spiral Cooling Towers
The innovation in industrial spiral cooling towers is driven by the ever-evolving needs of industry, particularly in the realms of energy efficiency and sustainability. The future of these cooling solutions looks promising with advancements in technology, including:
1. Smart Technology Integration
The incorporation of smart sensors and artificial intelligence will allow for improved monitoring of operational efficiency. Real-time data analytics can lead to proactive maintenance and performance optimization.
2. Eco-Friendly Designs
As sustainability becomes increasingly vital, designs that incorporate environmentally friendly materials and lower energy consumption will take precedence.
3. Enhanced Scalability
Future designs are expected to be more modular, allowing businesses to scale their systems up or down based on changing needs without extensive overhauls.
Conclusion
The rise of industrial spiral cooling towers signifies a pivotal development in the field of refrigeration equipment. These innovative cooling solutions not only provide efficiency and reliability but also support businesses in achieving operational excellence while being cost-effective. For companies like first-coldchain.com, investing in advanced cooling technologies like spiral cooling towers can lead to significant gains in both competitive advantage and sustainability. As industries continue to evolve, embracing such cutting-edge technologies will be crucial for success in the market.
© 2023 First Cold Chain. All Rights Reserved.